Meet ETA -Dynaform at NUMISHEET 2025
Join us in Munich, July 7–11, at the leading international conference on sheet metal forming simulation.
Visit our booth to explore how Dynaform is helping companies improve accuracy, efficiency, and material usage through powerful simulation tools.
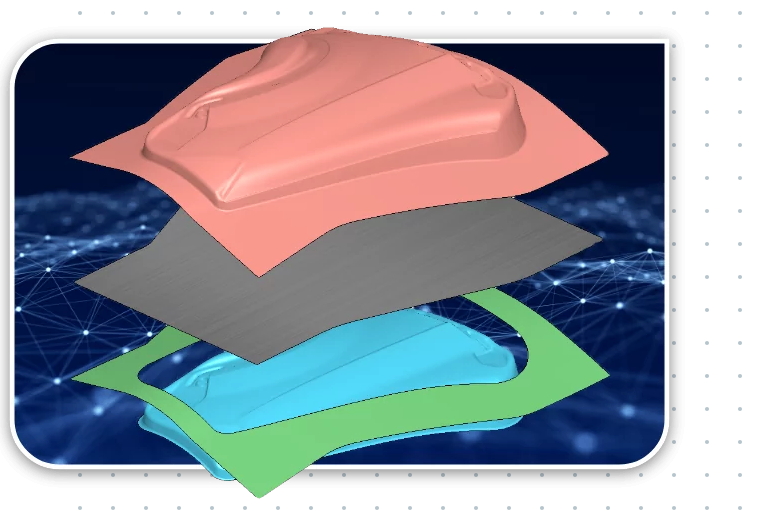
Unlock New
Possibilities
Next-Gen Features
Enhanced Performance
Redefining Standards

Dynaform - a complete sheet metal forming simulation software for die design and evaluation.
Dynaform is a general purpose sheet metal forming simulation software solution.
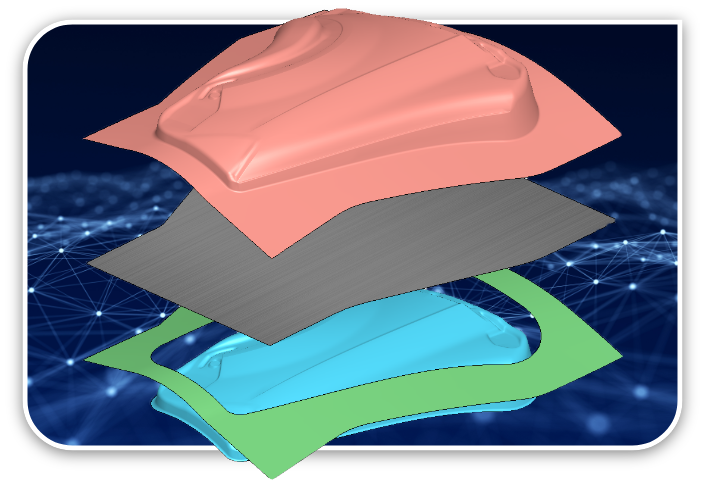
Dynaform Overview
Sheet Metal Forming Simulation Solutions
Dynaform® is a sheet metal forming simulation tool designed to improve all phases of the die development process. It allows an organization to entirely bypass soft tooling, reducing overall try-out time, lowering costs, increasing productivity and providing complete confidence in die system design. It also allows evaluation of alternative and unconventional designs and materials for an optimal solution. The most cost-effective and accurate solution available, DYNAFORM is the clear choice among progressive organizations seeking to streamline the die analysis system.
DYNAFORM encompasses the entire die system process in one simple interface.
By simulating every detail during the design stage, DYNAFORM ensures the highest quality formed part and best manufacturing process. The system guides the engineer through cost estimation, quoting, die evaluation and formability analysis. Then in a virtual environment, moves the part through the stamping process inside the plant—station by station.
Key Features of Dynaform®
- Comprehensive Simulation: Encompasses the entire die system design process in a single interface.
- Accurate Multi-Stage Formability Analysis: Ensures the highest quality formed part and optimal manufacturing process.
- Solver: Includes Sigform, an explicit finite element solver for sheet metal applications which is fast and accurate. Dynaform also supports the industry-standard LS-DYNA solver for reliable and robust simulations results.
- Cost Reduction: Bypasses soft tooling, reducing overall try-out time and costs.
- Productivity Boost: Increases productivity by streamlining the die development process.
- Design Flexibility: Evaluates alternative and unconventional designs and materials.
- Cost Estimation & Quoting: Guides through cost estimation and quoting for efficient project planning.
- Affordability: Leader in price-performance bracket, offering the most cost-effective and accurate solution available.
Blank Size Engineering (BSE)
Die Face Design (DFD)
Formability Simulation (FS)
Blank Trim Line Development (BTD)
Blank Size Engineering
A quick & easy process to check formability results & estimate manufacturing costs.
Unfold 3D sheet metal designs, estimate blank size, reduce scrap.
Accurately estimate blank size. Minimize scrap & piece costs.
BSE is a complete solution for accurately estimating blank size along with blank nesting for maximum material utilization, minimum scrap and piece costs. Using streamlined procedures, this powerful module allows the user to predict thinning, thickening, thickness strain, major prin. strain, min prin. strain, strain tensor & generate a forming limit diagram (FLD).
Blank Size Engineering is used to generate the blank outline, estimate product trimming line and nesting blank layout. It is equipped with the modified one step code, MSTEP for the rapid stamping simulation. The user may generate quick formability report for the product after conducting BSE simulation. MSTEP is improved to estimate sheet forming feasibility during the part design and development cycle, while which allows the user to quickly and accurately predict the blank size. The BSE enables users to quickly estimate the trim line of complicated parts. The improved blank nesting function optimizes the nesting result. For nesting of complicated parts, the result yields higher material utilization rate and more practical nesting layout.
Key Features of Dynaform®
- Comprehensive Simulation: Encompasses the entire die system design process in a single interface.
- Accurate Multi-Stage Formability Analysis: Ensures the highest quality formed part and optimal manufacturing process.
- Solver: Includes Sigform, an explicit finite element solver for sheet metal applications which is fast and accurate. Dynaform also supports the industry-standard LS-DYNA solver for reliable and robust simulations results.
- Cost Reduction: Bypasses soft tooling, reducing overall try-out time and costs.
- Productivity Boost: Increases productivity by streamlining the die development process.
- Design Flexibility: Evaluates alternative and unconventional designs and materials.
- Cost Estimation & Quoting: Guides through cost estimation and quoting for efficient project planning.
- Affordability: Leader in price-performance bracket, offering the most cost-effective and accurate solution available.
Dynaform Overview
Sheet Metal Forming Simulation Solutions
By simulating every detail during the design stage, DYNAFORM ensures the highest quality formed part and best manufacturing process. The system guides the engineer through cost estimation, quoting, die evaluation and formability analysis. Then in a virtual environment, moves the part through the stamping process inside the plant—station by station.
Contact us
Our team of CAE experts are ready to discuss your needs and how we can help solve your problems through the right product, our engineering services, or in-client resources.
or call us at 1-248-729-3010