Dynaform - a complete sheet metal forming simulation software for die design and evaluation.
Dynaform is a general purpose sheet metal forming simulation software solution.
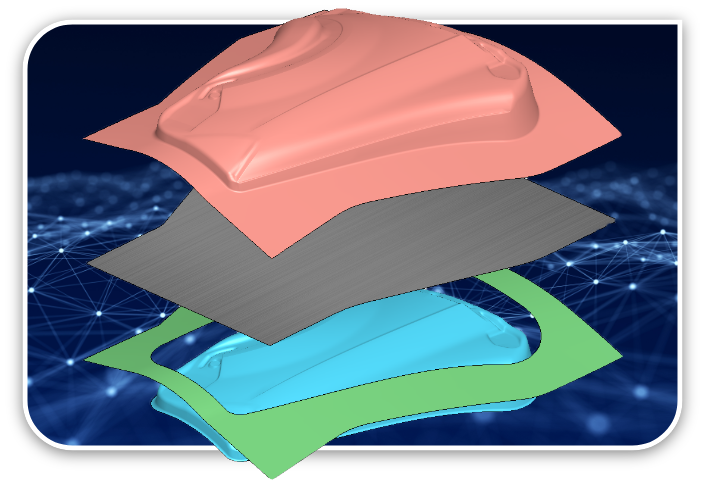
Dynaform® is a sheet metal forming simulation tool designed to improve all phases of the die development process.
Dynaform encompasses the entire die system process in one simple interface. Simulating every detail during the design stage, Dynaform ensures the highest quality formed part and best manufacturing process. The system guides the engineer through cost estimation, quoting, die evaluation and formability.
Die Face Design
Increase process reliability, efficiency, and cost reduction by bridging and streamlining the estimation and tool-building processes
Blank Size Engineering
Unfold 3D sheet metal designs, estimate blank size, reduce scrap.
Formability Simulation
Generate formability results, prevent costly manufacturing issues.
Die Evaluation
Die surface evaluation & modification, trimline and scrap size check.
Die System Analysis
Die structure analysis, scrap flow simulation, sheet metal transfer & handling.
Blank & Trimline Dev
Near net shape simulation to accurately predict blank & trimline.
Tube Bending & Forming
Simulation of CNC bending and hydroforming of tubular products.
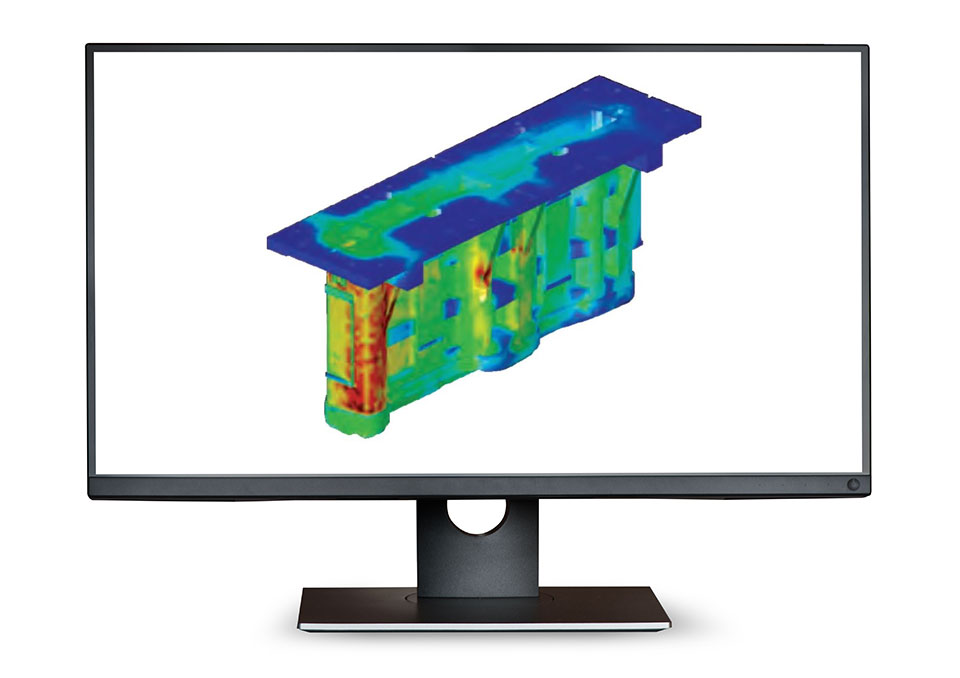
Dynaform 7.1 Introduces Die Face Design Capabilities
A quick-and-easy die face design enables a more accurate, more robust estimation process.
Die Face Design increases process reliability, efficiency, and cost reduction by bridging and streamlining the estimation and tool-building processes.
Die Face Preparation
Surface edit tools aiding user in generation of binder and addendum with Dynaform 7.1.
Binder Creation
With Flat, Profile, and Manual options, users can create best-fit binder for process and die surface.
Addendum Creation
Create addendum swiftly and as intricately desired, using different addenda profile features.
Die System Simulation Solution
Dynaform makes it possible to completely bypass soft tooling, reduce overall tryout time, lower costs, increase productivity and provide complete confidence in die system design. Makes possible evaluation alternative designs and materials.
Prevent Costly Errors
Go beyond just ID’ing issues. Actually improve performance & quality by reducing wrinkling, thinning & tearing.
Generate Quotes Quickly
Accurately estimate blank size and blank nesting for maximum material utilization, minimum scrap, and piece costs.
Rapid Reliable Results
Die Evaluation includes INCSolver, allowing engineers to generate reliable formability results with a short response time.
Uncover Flaws & Optimize Product Designs
Promote rapid development & validation of single-station and progressive die designs based on accurate LS-DYNA® results.
Complete multi-stage tube forming simulation
Dynaform’s tube forming simulation now supports multi-stage tube forming, including tube bending, tube pre-forming, tube hydroforming, trimming, and annealing. The simulations can accurately predict failures like wrinkles, cracks, spring back, and feasibility of hydroforming. No matter what process you are using or which stage you are focusing on, you can easily find the function you are looking for.
Full-process Tube Forming
Key tube forming processes include features like bending, preforming, hydroforming, trimming, and annealing.
Auto-Tool Creation
Robust automated tool creation based on product geometry.
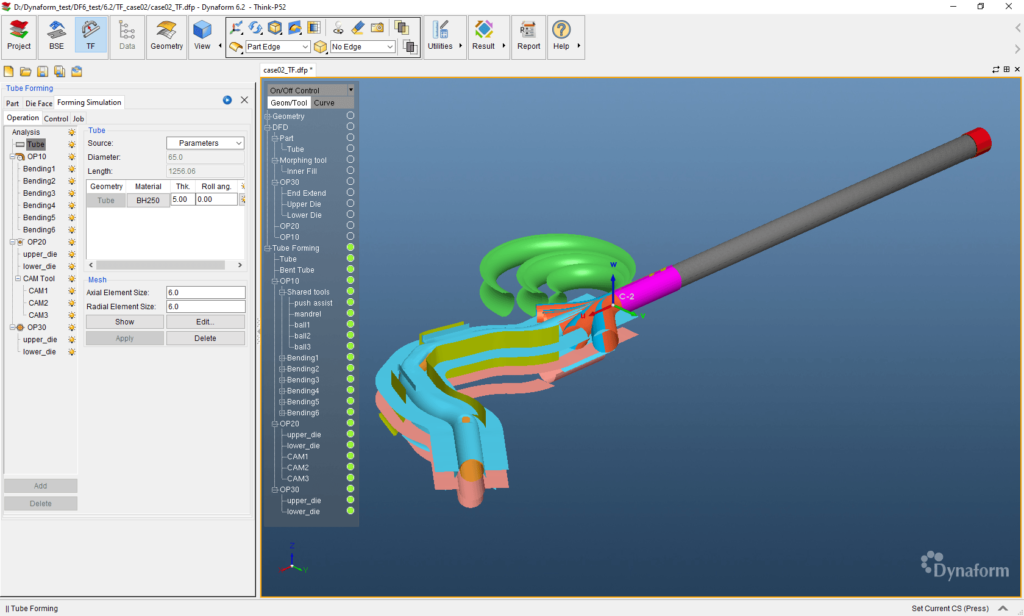
Bending table enhancements
Dynaform’s bending table now supports editing, inserting, and deleting operations. Users can now also import the bending table manually or automatically generate it from the center line. Our bending table generation algorithm improvements now serve to save users significant amounts of time generating tables.
Enhanced Simulation
Simulate tube feeding, rotating, and bending simultaneously.
Data Exchange
Enjoy seamless data exchanges with bending machines.
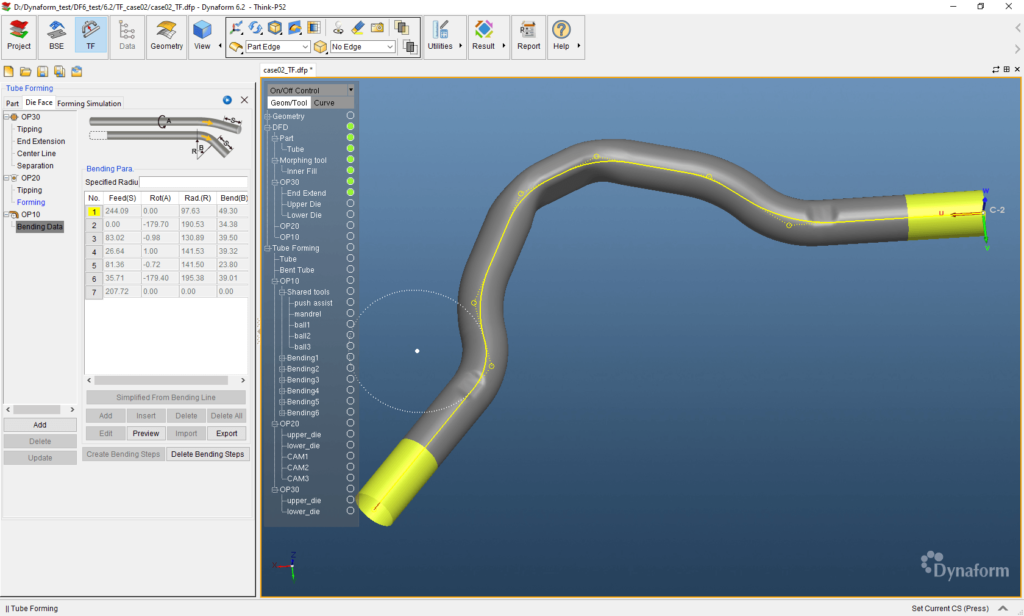
Next-generation hydroforming
Hydroforming in Dynaform 7.1 now supports comprehensive die face design including tube end extensions, centerline auto calculating, quick generating of die separating lines, mesh model separation based on separating lines, and more. Instead of switching to CAD software to create the tools, users can finish almost all major FEA model preparation works in Dynaform.
FEA Preparation
Finish motion definition, mesh editing, & more – all in Dynaform.
Tools Generation
Generate both upper and lower tools quickly and easily.
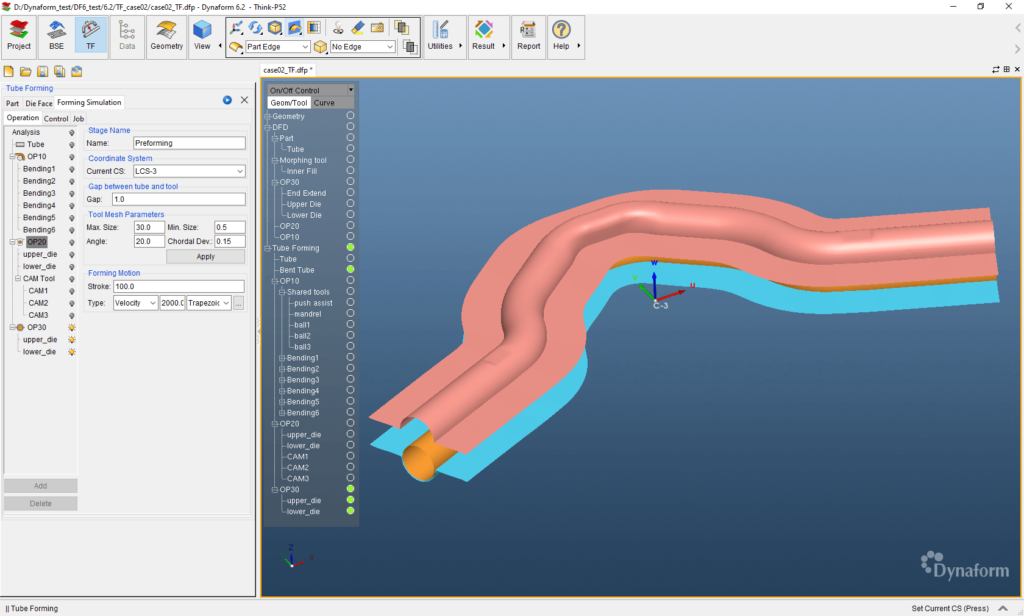
Key Dynaform modules include BSE, FS, D-Eval, and DSA. Use one or all.
Dynaform’s sheet metal forming simulation software makes it possible to uncover design flaws early in the process. Using the various modules engineers can more-fully evaluate alternative–and unconventional–designs. Doing so helps ensure higher quality outcomes.
Blank Size Engineering
Accurately estimate blank size. Minimize scrap & piece costs.
Simulate Formability
Forming Limit Diagrams indicate major strain and problem areas.
Early CAD analysis
D-Eval module analyzes CAD-based tooling during the early stages.
Got Scrap?
Use DSA mod to overcome shutdowns due to scrap removal failures.
What's new in Dynaform 7.1
Dynaform 7.1 is the streamlined die simulation solution designed for today’s highly competitive markets and unsettled economic conditions.