By Curtis Hsiung, Technical Sales Representative
The Stamping tool and die industry has evolved tremendously over the last few decades. Industry standards went from hand-sketching physical drawings of tools to having a plethora of CAD software at your discretion to develop models, complete sheet metal forming simulations, and design tools.
Nowadays, it is uncommon to see tooling designs developed and refined through hand drawings, because designing through CAD software not only can produce accurate drawings themselves but can also save engineers a lot of time.
Similarly, we went from experienced tool and die makers physically designing dies to having the years of experience and wisdom being passed down to reliable simulation software that can save time and costs on reworking and retooling.
Dynaform is a stamping simulation tool that can be critical to the success of your stamping production cycle by providing you with reliable and accurate results while saving you time and money in your production cycle.
What is Dynaform FS Module?
ETA’s Dynaform FS Module is a combined pre-and-post processor designed just for the sheet metal stamping process. It gives users the ability to set up their stamping process with imported CAD tools, simulate their stamping process with correct materials & tooling movements, and provide users with applicable results.
These include FLD overview, thinning and thickening, spring back, and draw-in. Depending on the issue a user is dealing with, they can change tooling pressure, draw bead strength, or even compensate for spring back.
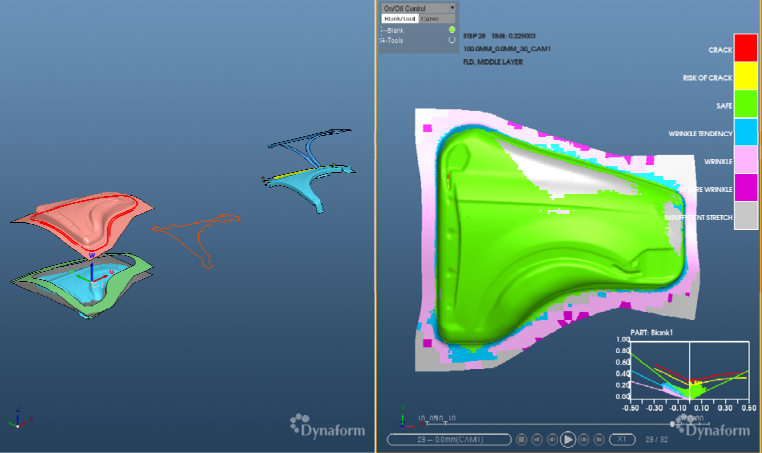
Why Dynaform’s FS Module over other sheet metal forming simulations software?
Dynaform’s FS Module couples ETA’s 40 years of experience in the stamping industry with the most reliable and realistic simulation solver, LS-DYNA. The FS module provides an efficient and streamlined workflow to set up your process. In just a few minutes, you can import your tooling, select your stamping process type and material, set up tooling motion, and submit the simulation to LS-DYNA.
LS-DYNA proves to be a dependable and potent solution for decades by providing trusted results in just about any real-world problem that you can set up in a simulation. From name-brand OEMs to local tool and die shops, Dynaform users rely on safe LS-DYNA simulation results to aid them in the stamping production cycle.
Who in the stamping production cycle should use Dynaform’s FS Module?
Dynaform’s FS Module can be used by quoting engineers, tooling design engineers, and tooling engineers on the production floor. Quoting engineers in the tool and die industry utilize Dynaform to quote jobs. By simulating the tools provided by their customers, they have a better idea of how much time and resources they will need to put in for the project they are quoting, ensuring their profit margins.
Tooling design engineers can simulate the process with the tools that they have developed and make necessary changes if the simulation results in surface defects or spring back that is out of spec. Tooling engineers on the shop floor can use the process set up in Dynaform to run the tryout process and use the LS-DYNA simulation results to help guide them in the right direction for tooling reworks.
Here at ETA, we are excited to partner with you to help make your stamping production cycle more efficient, saving you time, money, resources, and headaches, so that you can take on and finish more high-quality projects, faster. If you would like to see a demo or learn more, please visit us at https://www.eta.com/products/dynaform/.