While it is done early in the design process, the process of unfolding a sheet-metal part has considerable implications that can impact later product-cycle stages as well.
The unfolded blank information is related to the project’s cost estimation early on, the tooling setup in process engineering, and it often affects the final part boundary, which is a crucial factor in a successful assembly process.
While many CAD software out there can do a simple unfold on the part, few can do it with great accuracy, as to provide reliable job quoting, tooling, and part assembly.
In this 3-part blog post series, we will explore how different Dynaform modules can assist its users in achieving more accurate material cost estimation, reducing tooling recuts, and consistently creating parts within part-boundary spec.
Unfolding in Dynaform
Whether you estimate blanking by hand calculation, CAD unfold functionalities, or utilize other simulation software, Dynaform Blank Size Engineering (BSE) module is a powerful yet affordable tool that can help you bid and produce reliably.
Part Unfolding
With just a few clicks to define the part geometry, material, and thickness, a simple part can be unfolded, and its blank can be used further in quote estimation and process engineering.
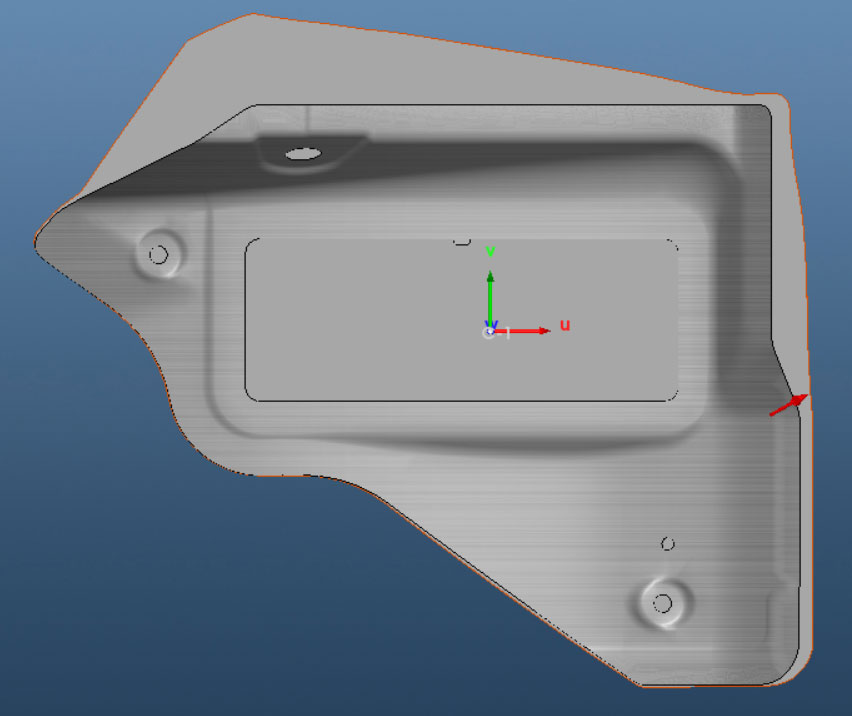
Formability Reports
Moreover, a formability report can be generated with the result variables of choice, such as FLD, major strain, thinning, etc…
Advanced Blanking Options
What if my blank is 2-out, you might ask? Our advanced blanking options has that covered as well. Simply choose the symmetry plane of choice with desired plane offset, insert the double fill, and unfold.
Symmetry Options
Other symmetry options, such as half-input and full-input symmetry, are available in addition to TWB (Tailor Welded Blank) and patchwork-blank blank types. Boundary holding conditions can also be considered when unfolding the blank, should you choose to do so.
Summary
The comprehensive, advanced blanking options offer users the flexibility and specificity to model their blanks the way users intend them based on the process-engineering blueprint they have in mind.
Now that the blank is accurately unfolded and defined, it is time to engineer a nesting layout that maximizes material utilization to minimize cost and waste.
In the next part of this 3-part blogpost series, we will explore Dynaform’s nesting functionalities for the conventional transfer die and Dynaform’s strip concept functionalities for the progressive-die setup for the now-unfolded blank.